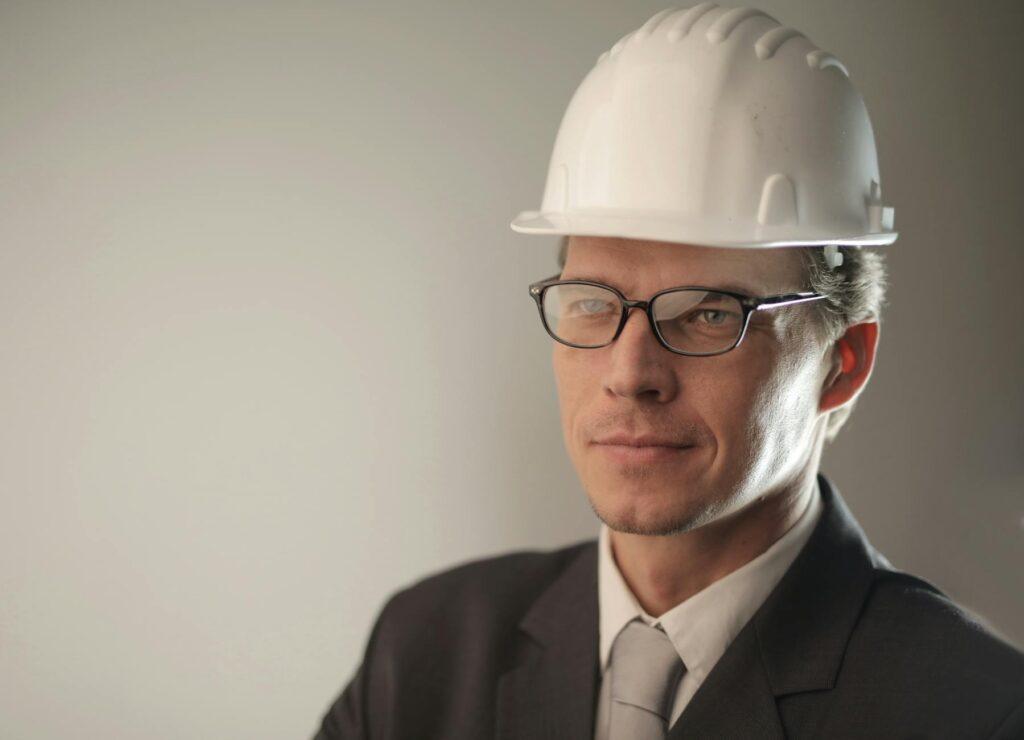
Introduction:
Navigating a career in Total Quality Management Systems (TQMS) within the automobile industry requires a unique blend of technical expertise, strategic vision, and leadership skills. Whether you’re preparing for an interview or looking to improve your knowledge, understanding the key questions and ideal responses can set you apart. In this article, we present the top 20 interview questions for TQMS managers, along with expert answers that cover essential principles, industry standards, and real-world applications. Dive in to enhance your preparation and succeed in your next TQMS interview.
General Questions
1. Tell us about your background and experience in quality management, particularly in the automobile industry.
Answer: I have over 15 years of experience in quality management, primarily within the automobile industry. My career began as a Quality Engineer at XYZ Motors, where I focused on improving production line processes and reducing defect rates. Over the years, I progressed to roles such as Quality Assurance Manager and eventually Quality Director. In these roles, I have managed quality systems, implemented continuous improvement initiatives, and ensured compliance with industry standards such as ISO/TS 16949 and IATF 16949. My experience spans both domestic and international operations, including managing supplier quality, conducting audits, and leading cross-functional teams to enhance overall product quality.
2. What motivated you to pursue a career in Total Quality Management?
Answer: My motivation to pursue a career in Total Quality Management (TQM) stems from a passion for problem-solving and a commitment to excellence. I have always been intrigued by the impact of quality on overall business performance and customer satisfaction. During my early career, I witnessed firsthand how effective quality management can transform production processes and drive significant improvements in efficiency and product reliability. This inspired me to delve deeper into TQM principles and methodologies, aiming to contribute to building products that meet the highest standards of quality and safety in the automobile industry.
Technical Questions For Quality Manger
3. Can you explain the core principles of Total Quality Management (TQM) and how you have applied them in your previous roles?
Answer: The core principles of TQM include customer focus, continuous improvement, employee involvement, process approach, and fact-based decision-making. In my previous roles, I applied these principles by:
- Customer Focus: Regularly gathering and analyzing customer feedback to align quality objectives with customer expectations.
- Continuous Improvement: Leading initiatives such as Kaizen events and Six Sigma projects to eliminate waste and improve processes.
- Employee Involvement: Encouraging participation in quality circles and providing training to empower employees to take ownership of quality.
- Process Approach: Mapping and standardizing key processes to ensure consistency and control.
- Fact-Based Decision Making: Utilizing data analytics and performance metrics to drive quality improvements and make informed decisions.
For example, at DEF Motors, I led a Six Sigma project that reduced the defect rate in the assembly line by 30%, significantly improving product quality and operational efficiency.
4. Describe your experience with various quality standards and frameworks, such as ISO/TS 16949, IATF 16949, or Six Sigma. How have you implemented these in your past roles?
Answer: I have extensive experience with quality standards such as ISO/TS 16949, IATF 16949, and Six Sigma. In my role at GHI Automotive, I led the transition from ISO/TS 16949 to IATF 16949, ensuring that all processes met the new requirements. This involved updating documentation, training staff, and conducting internal audits to verify compliance. Additionally, I have implemented Six Sigma methodologies to drive process improvements. At JKL Motors, I oversaw a Six Sigma project to improve the painting process, which resulted in a 20% reduction in paint defects and significant cost savings. My approach includes integrating these standards into daily operations, ensuring continuous compliance and leveraging their frameworks for continuous improvement.
5. How do you approach process improvement in an automotive manufacturing environment? Can you provide an example of a successful project you led?
Answer: I approach process improvement by first conducting a thorough analysis of current processes to identify bottlenecks and inefficiencies. I use tools like Value Stream Mapping (VSM) and Failure Mode and Effects Analysis (FMEA) to understand the root causes of issues. I then form cross-functional teams to brainstorm and implement solutions. For example, at MNO Automotive, I led a project to improve the efficiency of the engine assembly line. We used Lean principles to streamline workflows and eliminate waste. This project reduced assembly time by 25% and improved the overall equipment effectiveness (OEE) by 15%. Key to the success was involving employees at all levels and ensuring they were part of the solution process.
6. What tools and techniques do you use for quality control and quality assurance in automobile manufacturing?
Answer: For quality control and quality assurance, I use a combination of statistical process control (SPC), root cause analysis (RCA), and control charts. I also utilize quality management systems (QMS) software to track and document quality metrics. Techniques such as 5S, 5 Whys, and Fishbone Diagrams help in identifying and addressing issues. Additionally, I implement regular audits, both internal and external, to ensure compliance with standards and continuous improvement. For instance, at PQR Automobiles, we implemented SPC tools to monitor critical dimensions in the machining process, which significantly reduced variation and improved product quality.
7. How do you ensure that supplier quality meets the required standards? Can you describe a time when you had to address a significant quality issue with a supplier?
Answer: Ensuring supplier quality involves rigorous qualification processes, regular audits, and close collaboration. I establish clear quality expectations and performance metrics for suppliers and conduct periodic reviews. In one instance at STU Motors, we faced a significant quality issue with a supplier providing brake components. I led a team to conduct a detailed audit of their processes, identified gaps in their quality control, and worked with them to implement corrective actions. We provided training and support to improve their quality systems. This collaborative approach resulted in a 50% reduction in defects and strengthened the supplier relationship.
Leadership and Management Questions
8. Describe your leadership style. How do you motivate and manage your team to achieve quality goals?
Answer: My leadership style is collaborative and empowering. I believe in setting clear goals, providing the necessary resources and support, and fostering an environment where team members feel valued and motivated. I encourage open communication and actively involve my team in decision-making processes. To achieve quality goals, I set challenging yet achievable targets and recognize and reward contributions. For example, at VWX Motors, I implemented a recognition program for innovative quality improvement ideas, which boosted morale and led to significant process enhancements.
9. Can you provide an example of a time when you had to manage a conflict within your team? How did you handle it?
Answer: At YZ Motors, there was a conflict between the production and quality assurance teams regarding responsibility for a recurring defect. To resolve this, I facilitated a series of joint meetings to openly discuss the issues and concerns of both sides. We conducted a root cause analysis together and established a clear action plan with defined roles and responsibilities. By fostering open communication and mutual respect, we not only resolved the conflict but also implemented a solution that reduced the defect rate by 40%.
10. How do you ensure continuous improvement and innovation in your quality management processes?
Answer: I ensure continuous improvement and innovation by fostering a culture of learning and collaboration. I encourage my team to stay updated with industry best practices and emerging technologies through training and professional development. We regularly conduct Kaizen events and brainstorming sessions to generate new ideas for improvement. Additionally, I implement systems for capturing and analyzing data to identify trends and areas for improvement. For example, at ABC Motors, we introduced a digital quality management system that provided real-time insights and enabled more proactive quality control, leading to continuous enhancements in our processes.
Problem-Solving and Analytical Questions
11. Describe a situation where you identified a major quality issue in the production line. How did you address it and what was the outcome?
Answer: At DEF Automotive, we identified a major quality issue with the alignment of components in the final assembly. This was causing significant rework and delays. I led a cross-functional team to conduct a detailed root cause analysis using tools like Fishbone Diagrams and 5 Whys. We discovered that the issue was due to inconsistent calibration of assembly fixtures. We implemented a standardized calibration process and provided training to the operators. This intervention reduced alignment-related defects by 70% and improved overall production efficiency.
12. How do you utilize data and analytics to drive quality improvements in production processes?
Answer: I use data and analytics to identify patterns, trends, and areas for improvement. By implementing statistical process control (SPC) and utilizing control charts, we can monitor process performance in real-time. I also leverage quality management software to collect and analyze data from various stages of production. For instance, at GHI Motors, we implemented a data-driven approach to monitor and analyze defects in the welding process. By identifying the root causes and addressing them, we reduced the defect rate by 25%. Data analytics also helps in making informed decisions and prioritizing improvement initiatives.
Strategic and Visionary Questions
13. What do you see as the future trends in quality management for the automobile industry? How do you plan to stay ahead of these trends?
Answer: Future trends in quality management for the automobile industry include the integration of advanced technologies such as artificial intelligence (AI), machine learning, and the Internet of Things (IoT) for predictive maintenance and real-time quality monitoring. There is also a growing emphasis on sustainability and green manufacturing practices. To stay ahead of these trends, I continuously invest in learning and professional development, attend industry conferences, and collaborate with technology partners. At JKL Motors, we have started integrating IoT devices for real-time monitoring of critical equipment, which has already shown promising results in reducing downtime and improving quality.
14. How do you align quality objectives with the overall business strategy of an automobile company?
Answer: Aligning quality objectives with the overall business strategy involves understanding the company’s vision, goals, and market position. I work closely with senior leadership to ensure that quality objectives support strategic initiatives such as market expansion, cost reduction, and innovation. For example, if the business strategy focuses on enhancing customer satisfaction, I set specific quality goals related to reducing defects and improving reliability. Regular communication and strategic planning sessions ensure that quality objectives are integrated into the broader business strategy and that progress is continuously monitored and adjusted as needed.
Behavioral and Situational Questions
15. Tell us about a time when you had to make a difficult decision related to quality management under tight deadlines. What was the situation and what did you decide?
Answer: At MNO Motors, we faced a critical situation where a batch of components failed quality inspection just days before a major shipment deadline. The easy decision would have been to pass the components with minor rework to meet the deadline, but I chose to halt production and conduct a thorough investigation. We discovered a flaw in the supplier’s material that could have led to significant customer issues. Although this decision delayed the shipment, it ultimately protected the company’s reputation and customer trust. We worked around the clock to rectify the issue, sourced alternative materials, and expedited production to minimize delays.
16. Describe a project where you successfully led a cross-functional team to improve a product or process quality. What were the challenges and how did you overcome them?
Answer: At PQR Automobiles, I led a cross-functional team to improve the quality of our new engine model, which was experiencing high defect rates. The challenges included resistance to change, lack of communication, and technical issues. We started by conducting a comprehensive root cause analysis and identifying key areas for improvement. We implemented regular communication meetings, involved team members from all departments, and provided targeted training. By fostering collaboration and transparency, we overcame resistance and technical challenges. The project resulted in a 40% reduction in defects and improved the overall performance of the engine.
Customer-Focused Questions
17. How do you ensure that customer feedback is integrated into the quality management process? Can you give an example where customer feedback led to a significant improvement?
Answer: Customer feedback is integral to our quality management process. We have established channels for collecting and analyzing customer feedback, such as surveys, warranty data, and direct customer interactions. This feedback is regularly reviewed and used to inform quality improvement initiatives. For instance, at STU Motors, customer feedback indicated issues with the durability of our vehicle seats. We conducted an in-depth analysis, identified the root causes, and worked with suppliers to improve the material quality and design. These changes significantly enhanced the durability and led to a notable decrease in customer complaints.
18. How do you balance the need for high-quality standards with the pressure to meet production deadlines and cost constraints?
Answer: Balancing high-quality standards with production deadlines and cost constraints requires strategic planning and efficient processes. I prioritize proactive quality planning and continuous improvement to prevent issues before they arise. This includes investing in training, process optimization, and robust quality assurance measures. For example, at VWX Motors, we implemented Lean manufacturing principles to streamline processes and reduce waste, which helped us maintain high-quality standards while meeting production deadlines and controlling costs. Clear communication and collaboration between quality and production teams ensure that we can address any conflicts and find solutions that meet both quality and business objectives.
Innovation and Adaptability Questions
19. Can you discuss a time when you introduced a new technology or method to improve quality in an automobile manufacturing process? What was the impact?
Answer: At XYZ Automotive, I introduced a real-time quality monitoring system using IoT sensors and data analytics. These sensors were installed on critical machinery to continuously monitor performance and detect anomalies. The data was analyzed in real-time, allowing us to identify and address issues before they led to defects. This technology significantly improved our ability to maintain consistent quality and reduced the defect rate by 20%. It also enhanced our predictive maintenance capabilities, reducing unplanned downtime and maintenance costs.
20. How do you stay updated with the latest advancements in quality management and automotive technologies?
Answer: I stay updated with the latest advancements by regularly attending industry conferences, participating in professional associations, and pursuing continuous education through workshops and certification programs. I also subscribe to industry journals and follow thought leaders in quality management and automotive technology. Additionally, I foster a culture of learning within my team by encouraging knowledge sharing and providing opportunities for professional development. At DEF Motors, we have established a quarterly innovation review meeting where team members present new technologies and methodologies that could benefit our processes, ensuring that we stay at the forefront of industry advancements.
Read More Article click here
For More services click here
- Top 15 MNCs Every Mechanical Engineer Dreams of Joining in 2025
- How to Digitize and Automate the CAPA Process
- Top 10 Essential Tools Every Mechanical Engineer Should Know
- What is GD&T (Geometric Dimensioning & Tolerancing) ?
- Principles of IATF 16949: A Guide to Quality Management
- The Evolution of IATF 16949: The Automotive Quality Standard
- Top Interview Questions Related to SPC ,Cp and Cpk
- Difference Between Purchase and Procurement
- Master Your Job Interview: Top 70 Common Interview Questions and Answers
- What Is Standard Deviation ?
- Top Interview Questions and Answers on SPC
- Top 20 Interview Questions For Customer Quality Manager ?