Built in Quality (BIQ)& Jidoka
Introduction
Quality is the cornerstone of any successful product or service. In today’s highly competitive market, businesses must focus on delivering top-notch quality to meet and exceed customer expectations. This article delves into the concept of “Built in Quality,” exploring how it can enhance your product’s excellence and elevate your business to new heights.
Understanding of BIQ:
Built in Quality refers to a proactive approach to product development and manufacturing. Instead of relying solely on inspections and quality control at the end of the production process, Built in Quality emphasizes integrating quality measures throughout every stage. By doing so, defects are prevented from occurring in the first place, saving valuable time, effort, and resources.
Base Philosophy:
Do not pass defects to the next process:
Team members shall have the skill to review the parts entering and outgoing their station to identify abnormal (and normal) situations; assure product meets the quality expectations before it goes to the next process. Whenever an abnormality is found, the process shall be stopped, help requested, and wait for condition go back to normal.
Identify the problem and apply countermeasures:
Manufacturing variation is normal; the key point is to maintain variation within the standard. Quality issues shall be identified, gaps clarified, there must be current and future countermeasures decided. Top 5 Quality Issues to be identified and ongoing countermeasures.
Team Member role:
The role of the team member is to follow standard work, assure the processes are maintained fully operational, identify problems, request support as needed. When a team member is absent, the team leader shall fill in the process or place a fully trained team member from another area. The Team Leader and Group Leader are responsible to control and assure Built in Quality at the process. Only trained Team Members are authorized to operate the process.
Principle of BIQ:
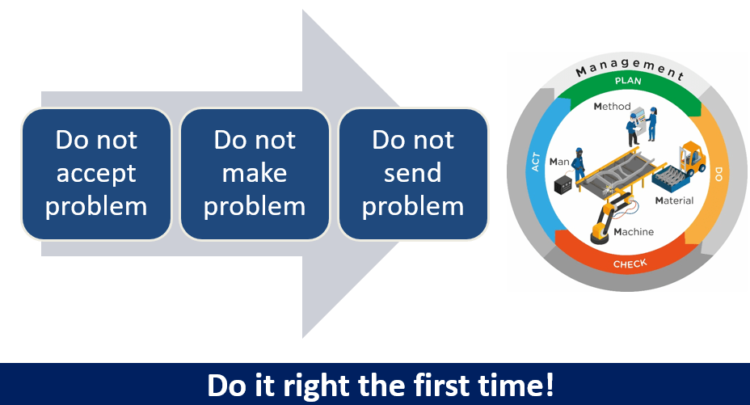
5M´s Approach:

Man :

- TM to be fully capable to perform the job at the process.
- Trained by Team Leader who assures zero quality flow outs.
- Skill level identified.
- Judgment of good/no good working in safe operation.
- TM can verbally tell you the process steps, key points, and normal/abnormal judgment regarding Quality and the process.
- Proper process order and use of all tools.
Material:
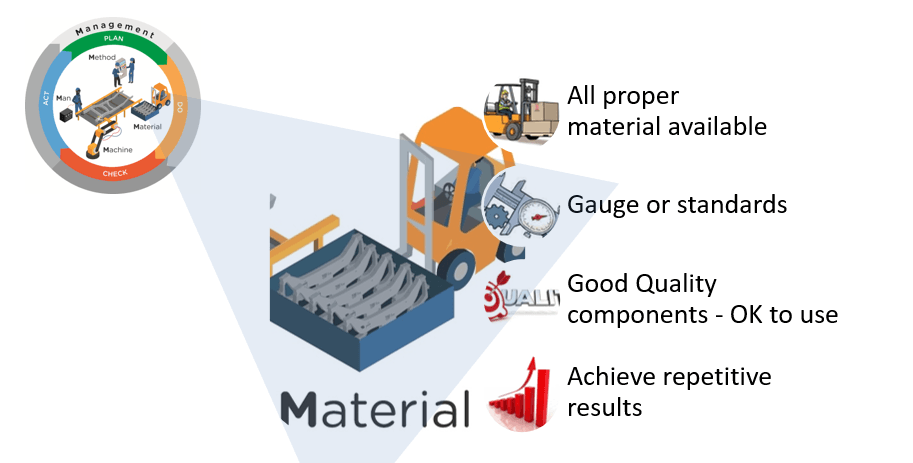
- All proper material available.
- Gauge or standards.
- Good Quality components.
- All tools to perform the work.
- Achieve repetitive results.
- Part identification on flow rack in and out.
- Quality requirements identified.
- Process completion identification.
- Traceability.
Method:
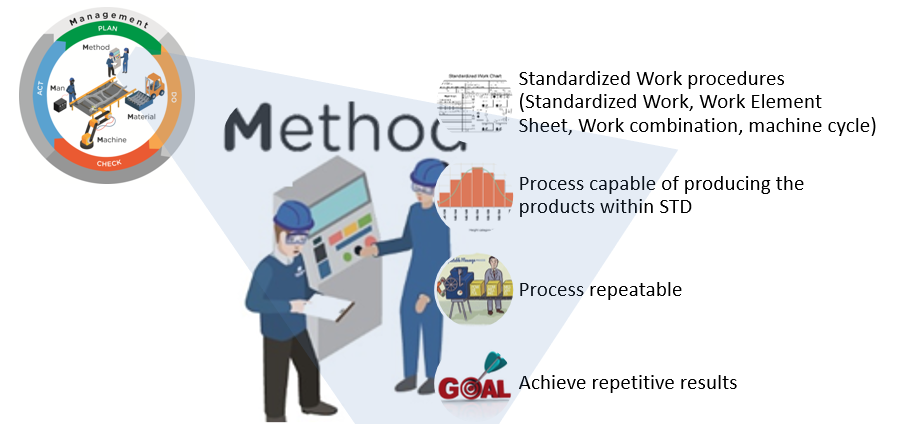
- Standard operation procedures (SW, Work combination, machine cycle).
- Process capable of producing the products within STD.
- Process repeatable.
- Achieve repetitive results.
- Process completion identification.
- Boundary samples, Good and No Good.
- Traceability.
- Reword Standard should be identified.
Machine:
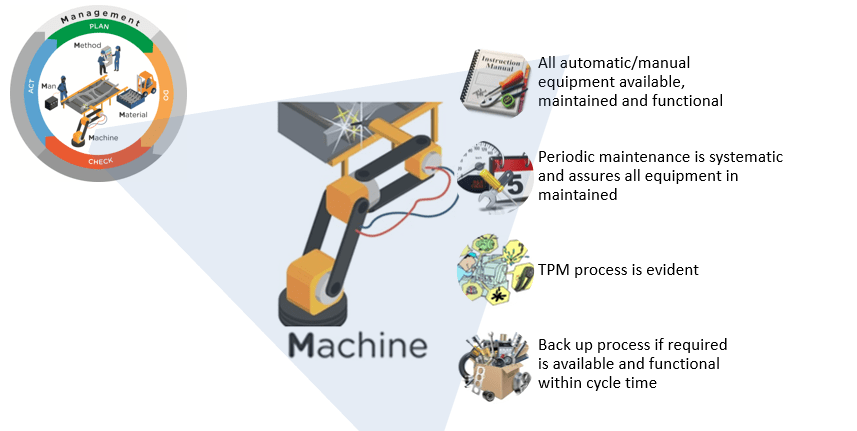
- All automatic/manual equipment available, they must be maintained and functional.
- Periodic maintenance is systematic and assures all equipment in maintained.
- TPM process is evident.
- Back up process if required to be available and functional within cycle time.
- Poka Yoke.
- Daily Check Production and Maintenance.
- Equipment is identified by Numbering System.
Management:
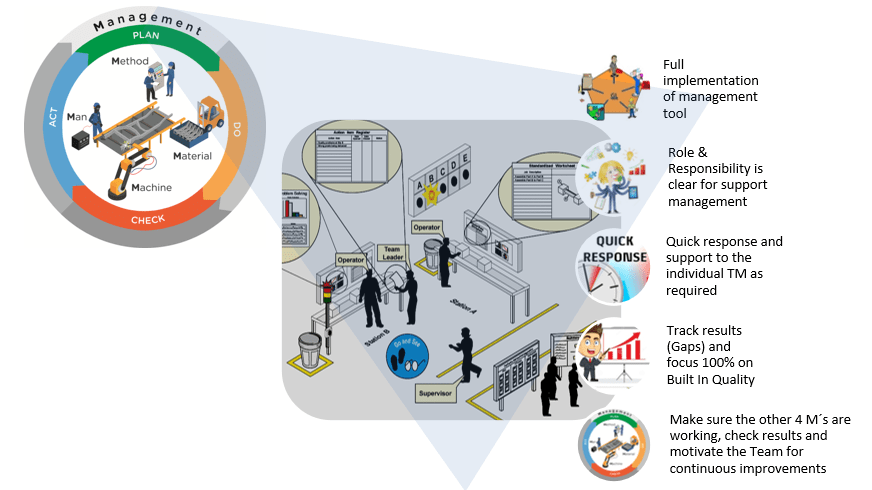
- Full implementation of management tool.
- Role & Responsibility is clear for support management.
- Quick response and support to the individual response and support to the individual TM as required.
- Track results (Gaps) and focus 100% in Built in Quality.
- Make sure the other 4 M´s are working. Check results and motivate the Team for continuous improvements.
- Process Operating System is established.
- Management follows the System.
- Production is supported and met by following the system.
- Management must lead by example and support the team.
Flow Out Prevention(Jidoka):
Flow Out Prevention, also known as Jidoka, is a concept and principle in Lean manufacturing that focuses on building quality into the production process and preventing defects from passing downstream. Jidoka is a Japanese term that can be translated as “automation with a human touch.”
The main idea behind Jidoka is to empower workers and machines to stop the production process immediately when a problem is detected. This allows for timely intervention and prevents the production of defective or faulty products. By implementing Jidoka, manufacturers can reduce waste, improve product quality, and enhance overall efficiency.
Key elements of Jidoka include:
Detecting abnormalities:
Installing sensors and checkpoints throughout the production process to identify any deviations from the standard or expected conditions.
Stopping production:
When an abnormality is detected, the production process is automatically halted to prevent the production of defective items.
Fixing the problem at the source:
Once production is stopped, workers investigate the issue, identify the root cause of the problem, and resolve it to prevent its recurrence.
Empowering workers:
Workers are not just responsible for performing tasks but are also encouraged to be vigilant and actively involved in monitoring and improving the production process.
By integrating Jidoka into the manufacturing process, companies can achieve higher levels of quality control, reduce the risk of defects reaching customers, and create a culture of continuous improvement. It also allows workers to take ownership of their work and contribute to the overall success of the organization.
Benefits of BIQ Implementation:
- Ensure customer satisfaction in quality, delivery and cost.
- Eliminate rework of critical parts.
- Reduce scrap identifying issues at source.
- Reduce variation of process ensuring standardized work at last level.
- Creating a higher morale among employees
Conclusion:
In conclusion, Built in Quality is a crucial aspect of modern business operations. By embracing this approach, companies can achieve unparalleled levels of customer satisfaction, optimize efficiency, and reduce costs. Investing in quality from the beginning is a strategic move that will pay dividends in the long run. So, let your mantra be “Built in Quality” and witness your products soar to new heights of excellence.
Pingback: 12 Barriers To Implementing Quality - Quality Corner
Pingback: Why Training Programs Fail - Quality Corner
Pingback: Next-Gen Quality Assurance: Use ChatGPT In Problem-Solving - Quality Corner
Pingback: Delight Your Customers: The Art of Customer-Driven Quality - Quality Corner