Cost Of Quality (COQ):
I. Introduction:
In the fast-paced and ever-evolving world of business, one factor remains constant: quality. The Economics of Quality (Cost of quality-COQ) is a concept that underscores the vital relationship between the quality of products and services and the economic aspects of an organization. Quality isn’t just a desirable trait; it’s a strategic imperative that can significantly impact a company’s bottom line, customer satisfaction, and competitive advantage.
In this article, we will delve deep into The Economics of Quality (Cost of quality-COQ) to understand its origins, components, implementation, measurement, challenges, and future trends. By the end of this journey, you’ll be equipped with insights to drive efficiency and excellence within your own business operations.
II. Understanding The Economics of Quality
A. Definition and Origins of COQ
The Economics of Quality (Cost of quality-COQ) originated from the realization that investing in quality can lead to substantial financial gains over the long term. It was formalized by Armand V. Feigenbaum in the mid-20th century to quantify the costs and benefits associated with maintaining and improving quality.
B. Components of COQ
COQ is comprised of four key components, each representing a category of costs that an organization incurs:

1. Prevention Costs:
These are the investments made to prevent defects from occurring in the first place. They include activities like employee training, quality planning, and process improvement initiatives.
2. Appraisal Costs:
These are the expenses incurred to assess and inspect products or services to ensure they meet quality standards. Examples include quality control inspections and testing.
3.Internal Failure Costs:
When defects are identified before reaching the customer, internal failure costs are incurred. These encompass the costs of rework, scrap, and retesting.
4.External Failure Costs:
These costs arise when defects make their way to customers. They involve warranty claims, customer support, recalls, and potential damage to a company’s reputation.
C. COQ as a Framework for Optimizing Resource Allocation
COQ serves as a strategic framework that helps organizations make informed decisions about resource allocation. By analysing the various components of COQ, businesses can identify areas where investments in prevention can yield significant cost savings in the long run.
III. The COQ Framework in Practice
A. Implementing COQ in Different Industries
COQ is applicable across a wide range of industries, from manufacturing to services. For instance:
1. In the manufacturing sector:
COQ principles have been successfully integrated into practices like Total Quality Management (TQM) and Six Sigma, resulting in reduced defects and increased operational efficiency.
2. In the service sector:
COQ has driven improvements in customer satisfaction through enhanced service quality and reduced service failures.
B. Case Studies Showcasing Successful COQ Implementation
Two prominent case studies highlight the impact of COQ in different industries:
1. Automotive Industry: Toyota Production System (TPS):
Toyota’s TPS, built on COQ principles, revolutionized manufacturing by emphasizing continuous improvement, waste reduction, and employee involvement. This approach led to exceptional product quality and streamlined processes.
2. Software Development: Agile Methodologies:
Agile methodologies in software development embrace COQ principles by encouraging iterative testing, early defect detection, and frequent collaboration. This results in higher-quality software and faster delivery cycles.
C. Benefits of COQ Adoption:
Implementing COQ(Cost of quality-COQ) can yield a multitude of benefits for organizations, including:
1. Cost Reduction through Waste Minimization:
By focusing on prevention and early defect detection, organizations can minimize rework and waste, leading to cost savings.
2. Enhanced Customer Satisfaction and Loyalty:
High-quality products and services result in satisfied customers who are more likely to become loyal brand advocates.
Improved Competitive Advantage and Market Positioning:
Superior quality sets an organization apart from competitors and positions it as a reliable and trustworthy choice in the market.
IV. Measuring and Calculating COQ
A. Metrics and Indicators for Each COQ Component
To measure Cost of quality-COQ effectively, organizations must establish relevant metrics for each component:
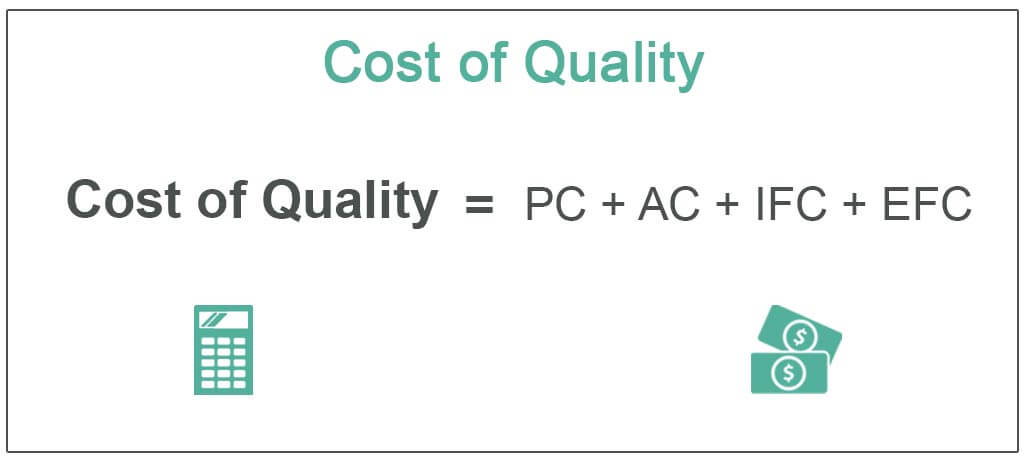
1. Prevention Costs:
Measure investments in quality training, process improvement projects, and quality planning initiatives.
2. Appraisal Costs:
Quantify expenses related to quality control, inspections, and testing activities.
3. Internal Failure Costs:
Track the costs incurred for rework, scrap, and retesting within the organization.
4. External Failure Costs:
Monitor expenses associated with warranty claims, customer support, and recalls.
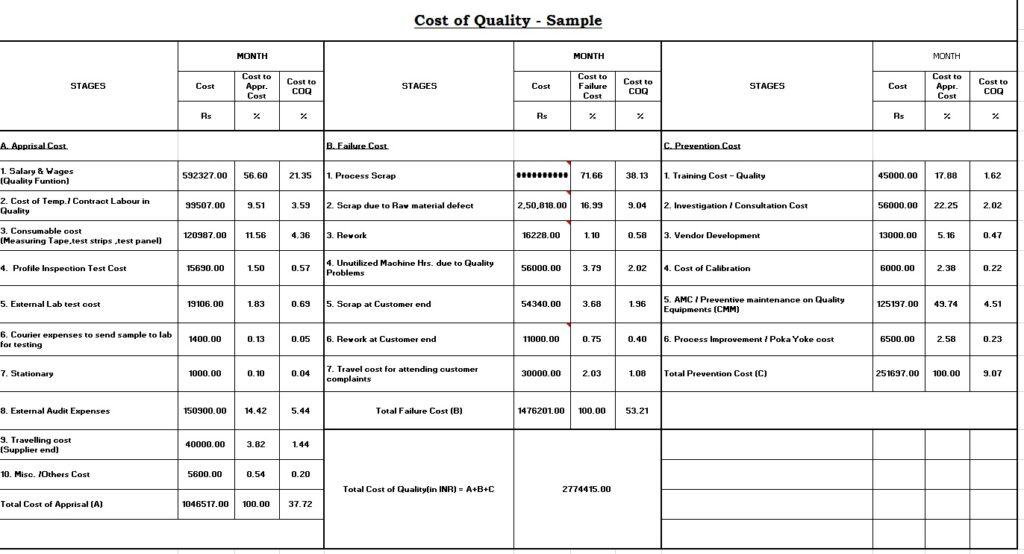
B. Establishing Benchmarks and Targets for COQ
Setting benchmarks and targets helps organizations gauge the effectiveness of their COQ initiatives. This involves comparing current COQ expenditures with historical data and industry standards to identify opportunities for improvement.
C. Steps to Calculate and Analyse COQ
Calculating COQ involves the following steps:
1. Gathering Cost Data:
Collect data related to the four COQ components from various departments and sources.
2. Assigning Costs to Respective Categories:
Distribute the collected costs into prevention, appraisal, internal failure, and external failure categories.
3. Interpreting COQ Results:
Analyze the COQ data to identify trends, cost drivers, and areas for improvement. This analysis informs strategic decisions on resource allocation and process enhancements.
V. Challenges and Considerations
A. Overcoming Resistance to Change
Introducing COQ might face resistance from employees accustomed to existing practices. Effective change management strategies, clear communication, and employee involvement can help overcome this resistance.
B. Balancing COQ with Other Business Priorities
Balancing COQ initiatives with other business priorities requires careful consideration. Organizations must align quality improvement efforts with overall strategic objectives to achieve a harmonious approach.
C. Addressing the Cultural Shift Towards Quality-Centric Mindset
Transitioning to a quality-centric mindset may require a cultural shift within the organization. Encouraging a culture of continuous improvement, collaboration, and accountability is essential to successfully embed COQ principles.
VI. Future Trends in COQ
A. Integration of Technology for Real-Time Quality Monitoring
Emerging technologies such as the Internet of Things (IoT) and Artificial Intelligence (AI) enable real-time monitoring of quality metrics. This integration enhances the ability to detect defects early and optimize processes for higher efficiency.
B. Sustainable Quality Practices and Environmental Impact
As environmental concerns continue to rise, businesses are incorporating sustainable quality practices into their COQ framework. This includes minimizing waste, reducing resource consumption, and ensuring eco-friendly production processes.
C. Evolving Customer Expectations and Their Influence on COQ
Customer expectations are evolving, with an increasing emphasis on ethical sourcing, transparency, and responsible manufacturing. COQ principles will need to adapt to meet these changing customer demands.
VII. Conclusion
In the complex landscape of modern business, The Economics of Quality (COQ) stands as a guiding principle to drive efficiency, elevate product and service quality, and achieve sustainable success. By understanding and implementing COQ, organizations can streamline operations, reduce costs, and build lasting customer relationships.
As we conclude our exploration of COQ, I encourage you to embrace this framework, assess its applicability to your industry, and embark on a journey of continuous improvement. By weaving quality into the very fabric of your business, you pave the way for a prosperous and impactful future.
Click below for similar topic
- Top 15 MNCs Every Mechanical Engineer Dreams of Joining in 2025
- How to Digitize and Automate the CAPA Process
- Top 10 Essential Tools Every Mechanical Engineer Should Know
- What is GD&T (Geometric Dimensioning & Tolerancing) ?
- Principles of IATF 16949: A Guide to Quality Management
- The Evolution of IATF 16949: The Automotive Quality Standard
- Top Interview Questions Related to SPC ,Cp and Cpk
- Difference Between Purchase and Procurement
Nice
Pingback: Delight Your Customers: The Art of Customer-Driven Quality - Quality Corner
Pingback: Next-Gen Quality Assurance: Use ChatGPT In Problem-Solving - Quality Corner