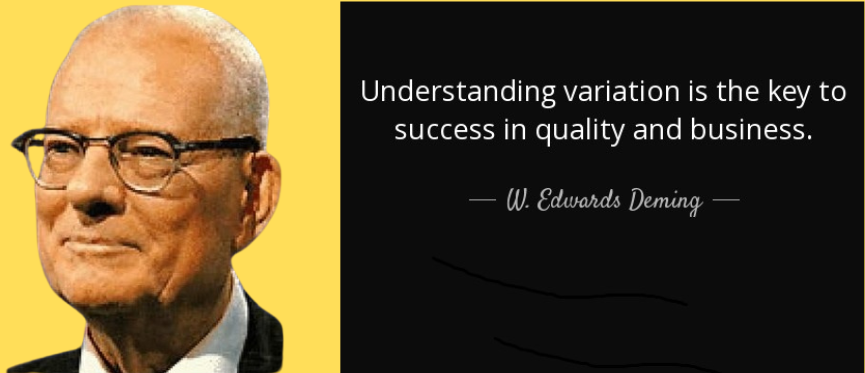
Understanding Variation:
Deming emphasizes that variation is inherent in every process and must be understood and managed for quality improvement. Variation refers to the differences in output or performance of a process. He categorizes variation into two main types:
- Common Causes (Systemic Variation):
- Definition: These are the inherent variations within a process caused by the system itself. They are random, predictable, and expected variations that occur naturally.
- Examples: Variations in raw material quality, environmental conditions, machine wear and tear, and inherent differences in human performance.
- Management Approach: To reduce common causes, systemic changes must be made. This involves improving the overall process, such as enhancing equipment maintenance, standardizing procedures, and improving training and materials.
- Special Causes (Assignable Variation):
- Definition: These are variations that arise from specific, identifiable sources that are not part of the normal process. They are sporadic and unpredictable.
- Examples: Machine malfunctions, human errors, defective materials, and unusual environmental factors.
- Management Approach: Special causes must be identified and eliminated by taking corrective actions. This could involve repairing equipment, retraining employees, or changing suppliers for raw materials.
The Importance of Distinguishing Between Common and Special Causes:
- Correct Diagnosis: Misinterpreting the type of variation can lead to incorrect actions. For example, treating a common cause as a special cause can lead to unnecessary adjustments and increased variation.
- Effective Solutions: Proper identification allows for appropriate interventions. Common causes require systemic changes, while special causes need specific corrective actions.
- Reducing Over-Adjustment: Also known as “tampering,” this occurs when managers make adjustments to a process based on random variations (common causes), which can worsen the situation.
Statistical Process Control (SPC):
Deming advocates for the use of SPC as a tool to monitor and control variation within processes. SPC involves the use of statistical methods to understand and manage process performance. Key elements include:
- Control Charts:
- Purpose: To distinguish between common and special causes of variation.
- Structure: Control charts plot process data over time against control limits, which are statistically determined boundaries.
- Interpretation: Points within control limits indicate common cause variation, while points outside control limits suggest special causes needing investigation.
- Process Capability:
- Definition: The ability of a process to produce outputs that meet specifications consistently.
- Assessment: Involves analyzing the spread and centering of process data relative to specification limits.
- Improvement: Enhancing process capability involves reducing variation (common causes) and ensuring the process is well-centered within specification limits.
Managing Variation for Quality Improvement:
- Data-Driven Decisions: Deming emphasizes making decisions based on data and statistical analysis rather than gut feelings or assumptions.
- Continuous Monitoring: Regularly using control charts to monitor processes helps detect issues early and maintain control.
- Employee Involvement: Training employees in understanding variation and SPC tools empowers them to contribute to quality improvement.
- Systemic Changes: Focus on improving the entire system rather than individual components to achieve significant quality gains.
The Impact of Managing Variation:
- Consistency: Reducing variation leads to more consistent and predictable process outcomes, enhancing product quality.
- Customer Satisfaction: Consistent quality meets or exceeds customer expectations, improving satisfaction and loyalty.
- Cost Reduction: Lower variation reduces waste, rework, and scrap, leading to lower operational costs.
- Competitive Advantage: High-quality, consistent products differentiate a company in the market, providing a competitive edge.
Conclusion:
Understanding and managing variation is a cornerstone of Deming’s quality philosophy. By distinguishing between common and special causes, using SPC tools, and focusing on systemic improvements, organizations can achieve higher quality, greater productivity, and improved competitive positions. Deming’s insights into variation management remain foundational in modern quality management practices.
- Top 15 MNCs Every Mechanical Engineer Dreams of Joining in 2025
- How to Digitize and Automate the CAPA Process
- Top 10 Essential Tools Every Mechanical Engineer Should Know
- What is GD&T (Geometric Dimensioning & Tolerancing) ?
- Principles of IATF 16949: A Guide to Quality Management
- The Evolution of IATF 16949: The Automotive Quality Standard
- Top Interview Questions Related to SPC ,Cp and Cpk
- Difference Between Purchase and Procurement